Lead Quality - Berlin, Deutschland - Varroc Engineering
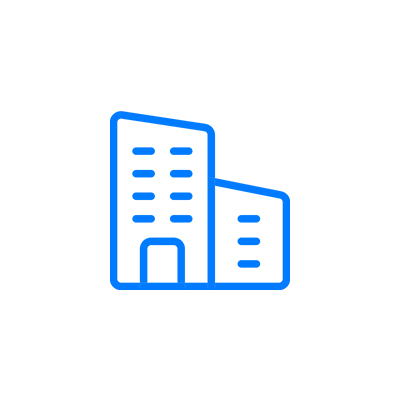
vor 3 Wochen
Beschreibung
Lead Quality
***
(QUA00550)
- Quality
- To be Filled***
About Us
Founded in 1988, Varroc group is a global tier-1 automotive component manufacturer and supplier of exterior lighting systems, plastic and polymer components, electricals-electronics components, and precision metallic components to passenger car, commercial vehicle, two-wheeler, three-wheeler and off highway vehicle ('OHV') OEMs directly worldwide.
With 36 world-class manufacturing facilities and 16 R&D centers in 10 countries, Varroc group is on an exponential growth trajectory clocking a sale of 1.5 billion USD in The company is one of the leading global passenger car lighting suppliers and amongst the top 2-wheeler automotive component supplier in India.
Varroc offers best design solutions that give customers a competitive edge in their markets.Ensure the adherence of Supplier Quality and In-coming Quality
Maintain Incoming parts quality, supplier monitoring and supplier audit
Be Part of CFT to have concrete AOI development with CD team during development.
Evaluate supplier product quality on regular basis and guide them to achieve consistency in quality.
Participate in supplier CAT Meeting.
Preparing and implementing supplier wise annual audit plan to improvement and evaluate the suppliers
Analyzing the audit report and action plan from supplier for closing NC's
Issue Supplier notification for quality issue, debit etc.
Adherence of quality systems at In-process Quality
Conduct the Internal audit of product & Manufacturing Processes and taking necessary corrective & preventive actions to prevent occurrences.
Review Layout testing and Functional testing for production process.
Enforce First off, last off, In-process product audit, control charts are implemented.
To ensure the Identification and traceability of parts during process and supplies to customer.
Maintain the QMS at Plant
Provide the details of Customer QMS requirements to Employees
Planning internal audit, coordinate to conduct management review meeting (MRM) & prepare minutes of meeting for necessary actions.
Carryout IATF internal audit as per plan in coordination with BU QMS lead.
Maintain QMS documents legibility & availability.
Implement Inspection standard and work instructions related to all QA process
Timely submission of revalidated reports and maintain layout inspection records etc.
Preparing the plan for process, product and poka-yoke Audit and analyzing audit report.
Preparing observation NCs report & tracking and verifying the actions against the NC's to ensure timely closure.
Achieve Zero defect out-flow to Customer
Control of master sample & revalidation.
Promote awareness of customer requirements throughout the organization.
Participate in APQP process.
Establish Quality control measures at the identified critical control parameters.
Ensure enough lighting is there in applicable parts checking area.
Control on outsourced processes.
Provide and check use of required PPEs to Shift Inspectors.
Set the competitive targets for Inspectors to improve Quality and productivity
Up-keeping available facility at Quality Lab
Monitor the calibration of measuring instruments as per plan
Controlling of measuring and testing equipment
To follow on testing with outside lab & maintaining the QA lab.
NPD Quality
Review control plans (Pre-launch and full production) and identify product design and process concerns during product planning stage.
Cross verify the documents (Setup approval/first piece approval/in process inspection/ final inspection/ dock audit)
Develop action plan to reduce vital RPNs through ME team (Above set baseline)
Be active member in CFT for development of Process documents during the Product Planning process (Gate 0) and all steps of DFMEA
Participate as CFT member to Calculate the SOD (Severity x Occurrence x Detection) number or risk priority number (RPN) as part of PFMEA
Communicate the importance of the implementation of QMS procedures to NPD (Program Management) and ensure alignment to VQS
Ensure the entire new product development process has quality assurance built in every step
Maintain the Customer Quality, Customer Complaint handling & IHR
Attending customer complaint & analyzing defect/abnormality as per customer feedback & keeping documentation of corrective measures.
Taking contentment action at customer end, warehouse & BSR. Doing root cause analysis & preparing action plan for taking corrective measures & horizontal deployments.
Updating the corrective measures in FMEA
Reporting to customer on process side & inspection side corrective action
Improve PPM at customer ends.
Participate in CAT meeting and reporting the action taken in timely manner to management and customers.
Attending planed /surprise customer audit.
Maintaining shop floor activities as per Customer Audit Check sheet in order to maintain customer audit score, product and process quality as per customers standard requirement (C
Mehr Jobs von Varroc Engineering
-
Shift Incharge
Berlin, Deutschland - vor 3 Wochen
-
Lead EHS
Berlin, Deutschland - vor 2 Wochen
-
HR Partner
Berlin, Deutschland - vor 3 Wochen
-
Category Buyer
Berlin, Deutschland - vor 1 Woche